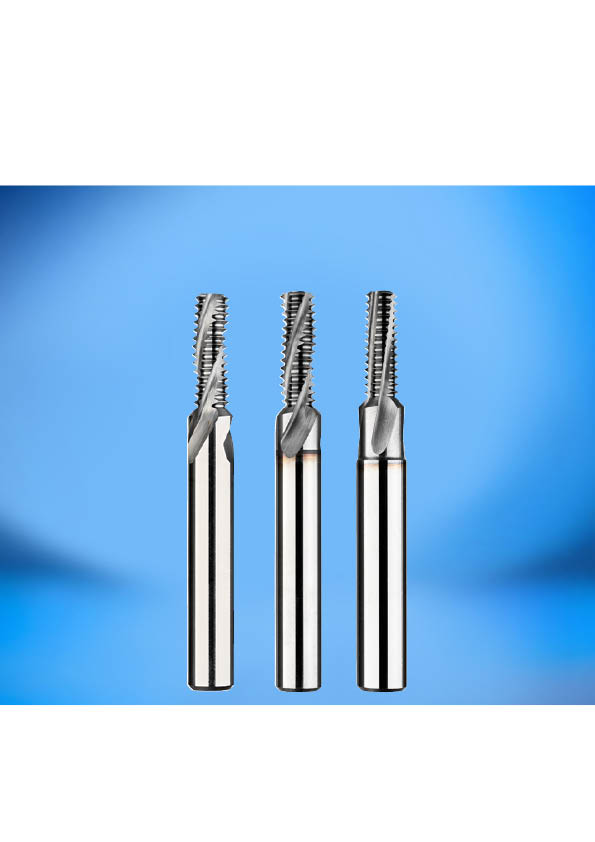
Best option
In many applications a Phantom tap, is a better solution. Thread milling is often the best option for thread creation in more difficult materials, larger diameters or unmanned production. The reduced risk of breakage, in particular, is a major advantage, especially in unmanned production. Thread milling is even preferable when creating a thread in very accurate workpieces, because the offset allows much better control of the dimensional accuracy than is possible with taps. For blind holes, the maximum thread length can be measured very accurately. In practice, thread milling has the advantage that you can mill several diameters with a single thread milling cutter as long as the pitch of the thread remains the same. This means that you can reduce the number of different tools in stock.
3 models
The demand for good thread milling cutters is growing. Phantom is therefore launching a complete range of solid carbide thread milling cutters for different applications. The basic model is a solid carbide Micrograin 2xD thread milling cutter in an uncoated finish. This tool is particularly suitable for occasional thread milling. The second model is the thread milling cutter with a TiCN coating which has two internal coolant feeds. This tool is also supplied in 2xD. The coating and internal cooling give better chip removal from the hole. This model is a typical thread milling cutter for production applications. An extra tool change is normally required to create a phase. This is not necessary in the third version of the Phantom thread milling cutter which has a phase for chamfering the edge. This cutter is also coated and has internal cooling. Phantom thread milling cutters are available with a pitch of 0.5 to 2.5 and for all current metric thread types.